Checkweighers
Introduction
Checkweighers automatically check the weight of products on a production line and can reject them based on predefined weight parameters.
They help maintain product quality, regulatory compliance, and operational efficiency. They can also be used in combination with Metal Detectors, x-rays or as part of a manual inspection process.
​
Key Functions
-
Weighing: Accurately measures the weight of products as they move along a conveyor belt.
-
Rejection: Automatically ejects products that do not meet weight specifications.
-
Data Logging: Records and tracks production data including weight, quantity, and rejects.
-
Accuracy: High precision, often within ±0.5g, with some models achieving ±0.2g.
-
Speed: Adaptable to various production speeds.
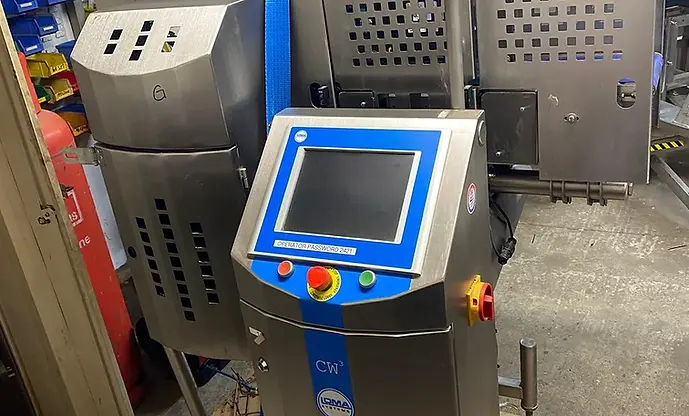
Types of Checkweighers
In-Motion Checkweighers
-
Designed for high-speed production lines.
-
Weighs moving products with automated reject systems for off-weight items.
-
Capable of handling speeds from 10 to 180 packs per minute.
Static Checkweighers
-
Used for manual checks of non-moving items or small batches.
-
Ideal for quality control and inventory management.
-
Typically used for spot-checking and compliance testing.
Checkcounting Scales
-
Combines weight measurement with counting capabilities.
-
Useful for managing large quantities of small components.
Combination Systems
-
Integrates additional features like metal detectors, X-ray systems, or vision inspection.
-
Provides comprehensive quality control and contamination detection in a compact unit.
Key Questions to ask when looking for a used food processing checkweigher
What are your weight requirements?
What is the weight range and precision needed for your to weigh your products?
What production speed do you need?
How many products do you need to weigh a minute?
Do you need to weigh different product sizes and shapes?
Are all your products the same, or will they change? Do you need the ability to set different weight parameters for different products?
What level of weight accuracy do you need?
Typically, checkweighers can measure to ±0.5g but can go as low as ±0.2g depending on your product.
Do you need more capabilities that just weighing?
Do you want to perform other tests at the same time, such as metal detection, or x-raying products?
What kind of reject system do you need?
Rejection of products can be automated, (such as pusher, pneumatic or air jets) or alarm and manual intervention.
How does the checkweigher integrate with existing your production line?
Does it need to run left to right? Are there any space restrictions? Is it standalone, or part of a product line? Are there any additional environmental concerns, such as moisture, temperature, dust)?
What is your budget?
Used Checkweighers can start in the low thousands and go upward from there, depending on age, condition, and the extra features it comes with.
​
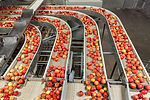